Advanced Driver Assistance Systems (ADAS) Calibration Services
Maintaining your truck fleet in top condition is quite simple. It all comes down to routine inspections, spotting issues before they escalate, assessing fleet status, and establishing prevention-focused methods. Regular inspections and repairs guarantee optimal uptime, enhanced productivity, and protection. Expert guidance from experts like Jim enables you to excel in fleet maintenance through the strategic application of digital tools, detailed logging, and qualified personnel. Go ahead, immerse yourself in the ultimate guide to fleet maintenance and unlock cost-effective operations. There's plenty to learn and uncover!
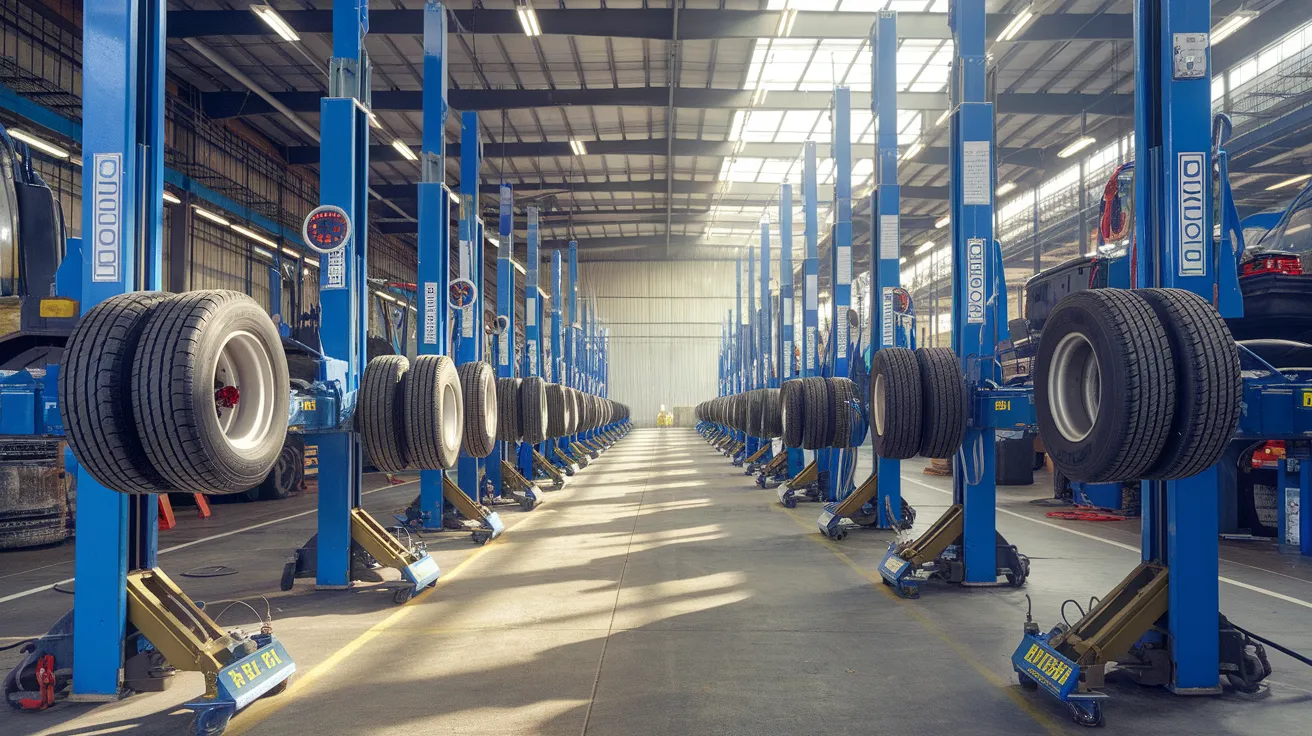
Essential Points
Recognizing the Importance of Scheduled Commercial Vehicle Service
Though it could feel overwhelming, getting a handle on proper fleet and truck maintenance is vital for any thriving operation. The benefits of maintenance greatly surpass your investment of time and energy. Consistent checks and upkeep can significantly extend the lifespan of your vehicles, preventing expensive replacements. Furthermore, there's a clear link between properly serviced vehicles and improved fuel efficiency. This results in decreased fuel spending, improving your overall cost efficiency. Furthermore, frequent maintenance can uncover minor issues before they escalate into major ones, preventing costly repairs later on. Therefore, don't underestimate the importance of routine maintenance; it can be a real game-changer for your operation's success.
Identifying Key Components of a Effective Maintenance Framework
To guarantee your fleet's efficiency and durability, it's critical to identify the fundamental aspects of a successful maintenance program. You'll have to grasp the basic principles of maintenance, track the health of your fleet consistently, and put in place preventive measures ahead of time. With these established, you're ready to decreasing downtime and optimizing productivity.
Key System Maintenance Requirements
When it comes to improve your fleet's performance and durability, creating a robust maintenance program is essential. Key components of the program consist of regular inspections, routine servicing, and preventive repairs. Each of these elements plays a crucial role in preventing costly breakdowns and reducing downtime. While the advantages of a maintenance program are substantial, you must consider the setup hurdles. These can range from operational difficulties and employee pushback. Nevertheless, with strategic organization, transparent dialogue, and dedication to training, these obstacles can be addressed. Remember that an effective maintenance program doesn't just resolve issues; it prevents them. It's an investment in your fleet's longevity – and it's one that delivers substantial benefits.
Fleet Condition Monitoring
As you delve into the key elements of a well-designed maintenance program, recognizing the importance of fleet condition monitoring takes center stage. It's not just about keeping your vehicles running, it centers on maximizing fleet performance. Fleet monitoring systems provide a thorough view of your fleet's condition, allowing you to detect potential issues prior to escalation.
These advanced systems monitor vital parameters like fuel performance, tire conditions, engine health, and more. By leveraging this data, you're not simply safeguarding the durability of your fleet but also saving on avoidable maintenance expenses. Note that timely discovery is crucial in fleet management. Thus, implement trustworthy monitoring solutions and stay ahead of the curve. Avoid simply responding to problems, predict them. Keep your fleet's condition in check and your operation will run smoothly.
Establishing Preventive Protocols
While monitoring your check here fleet's condition plays a vital role, putting preventive strategies in place is just as crucial to secure a robust maintenance program. You must identify potential problems before they transform into major repairs and equipment downtime. So, let's talk preventive measures.
An important measure is establishing a detailed maintenance checklist. This checklist should detail all necessary examinations, tune-ups, and component updates. Routine engine checks, tire rotations, and oil changes are a given. However, remember to check smaller components like windshield wipers, lighting systems, and filter components.
Your checklist should also include a timeline for all maintenance tasks. Adhering to this timeline ensures that your fleet stays in top shape. Keep in mind, preventative care reduces time, money, and headaches in the long run.
Essential Routine Checks for Transport Fleet Care
To ensure your truck and fleet stay in peak condition, you should emphasize regular maintenance inspections. These assessments encompass scheduled maintenance inspections and essential system reviews. By maintaining these crucial procedures, you'll extend your fleet's longevity, optimize operational efficiency, and ultimately, reduce expensive fixes.
Scheduled Service Checks
Routine maintenance inspections are your strongest line of defense against sudden fleet and vehicle failures. These inspections offer you the ability to identify and resolve concerns before they develop into major repairs or hazardous situations. One of the primary scheduled maintenance benefits is the avoidance of service interruptions, which can greatly impact your company's productivity and bottom line.
Key Component Evaluations
Following up on the significance of scheduled maintenance inspections, let's explore the particular essential component checks that must be carried out regularly to guarantee optimal truck and fleet performance. First examine the brake system – confirm all components are functioning efficiently, from brake pads to fluid levels, and checking for leaks. If ignored, brakes may malfunction, leading to catastrophic incidents. Tire pressure checks are equally crucial. Underinflation increases fuel consumption and tire wear, while over-inflation can cause a blowout. Purchase a quality pressure gauge for accurate readings. Keep in mind tires should be cold during checks for optimal results. Consistently conducting these important checks can save you from costly repairs and potential accidents. Maintain safety on the road.
Fleet Efficiency: Preventative Maintenance Best Practices
In fleet management, it's vital that you prioritize preventative maintenance to ensure peak efficiency. Establishing a well-structured preventative scheduling system is crucial. This reduces unnecessary wear and tear, and reduces the chances of unscheduled downtime. You must arrange regular maintenance and inspections based on mileage, time, engine hours, or fuel used. Keep in mind each vehicle is different and might need a customized approach.
Maintenance education serves as a crucial approach to ensure peak efficiency. Give your personnel the necessary skills to identify potential issues early on. This reduces downtime but also lowers operational costs. The fusion of preventative scheduling and maintenance training will result in a highly effective and reliable fleet. Remember, an ounce of prevention is worth a pound of cure.
Key Advice for Truck and Fleet Restoration and Repair
While truck and fleet repair and restoration may seem daunting, grasping the fundamentals makes it easier. Your starting point needs to be to understand multiple restoration approaches. This expertise will allow you to spot problems quickly and efficiently. Then, organize repair tasks depending on how serious the issues are and the vehicle's role in your operation. Routinely examine every truck for potential issues and tackle them quickly to prevent further damage. Don't forget, restoration isn't just about fixing issues, it's aimed at upgrading the vehicle's functionality and longevity. In conclusion, always use high-quality parts for maintenance; they'll last longer and perform better. Keep these tips in mind, and you'll manage truck and fleet repair and restoration successfully.
Harnessing Industry Innovations for Enhanced Fleet Management
To remain competitive in the trucking industry, it's vital to utilize innovative solutions for advanced fleet maintenance. New technologies are transforming the maintenance landscape. Make use of data analytics to analyze your fleet's operations and predict potential issues before they arise.
State-of-the-art monitoring systems can track and monitor engine health and efficiency, fuel consumption, and operator performance. Utilize this valuable information to plan preventive maintenance, decreasing costly operational interruptions.
Never ignore software updates. Such updates commonly include critical patches and enhancements that boost your fleet's operational efficiency and security. Keep in mind managing your vehicles isn't limited to mechanical care. You're conducting business in a technology-driven age, and staying current with market improvements will safeguard your fleet's sustainability and profitability. By utilizing effective systems, you can lower time and money, and potentially save lives.
Popular Questions
What Skills Should a Professional Fleet Service Technician?
You must have an official certification, fulfilling the criteria of an established mechanic institution. Additionally, you must pass a thorough skill assessment, showing your expertise in various aspects of fleet service and repair. Experience counts too!
What's the Right Time to Replace Fleet Vehicle Tires?
Just like the seasonal changes, it's important to inspect your fleet's tire wear on a consistent basis. Nevertheless, it's typically best to swap out tires every three to 6 years, according to driving conditions and frequency of use.
What Are the Common Signs of Engine Trouble in Trucks?
You can detect engine trouble in trucks from signs such as abnormal engine noises and poor fuel performance. Other signs include excessive smoke, fluid leakage, along with an illuminated check engine light that persists.
What Role Does Technology Have in Modern Truck and Fleet Maintenance?
Technology is fundamental in optimizing truck maintenance. Telemetry systems deliver real-time data, while analytical tools forecast issues before they happen. You'll notice less vehicle downtime, better safety measures and in the end, reduced expenses. It's revolutionary.
How Do Maintenance Needs Vary Across Fleet Vehicle Types?
Different vehicle types certainly require specific maintenance schedules. One must account for the intended use, load capacity, and driving conditions, as these factors significantly affect the necessary maintenance. Make sure to tailor maintenance according to the vehicle classification.
Final Thoughts
Ultimately, the focus is on keeping your fleet running smoothly, wouldn't you agree? Consistent upkeep isn't optional, it's absolutely necessary. By identifying key components, conducting routine checks, applying preventive maintenance approaches, and harnessing industry innovations, you're going beyond simple upkeep, you're crafting an efficient operation. And remember, fleet servicing isn't a problem, it's a pathway to enhancement. Stay committed, and you'll experience your fleet's productivity, consistency, and lifespan reach new heights.